Bertrand Debuisser, Director of Industrial Performance Consulting at HIVE Consulting and an alumnus of the MILES Master, helps us to understand this approach and the expected benefits for the company.
How would you define Lean Management?
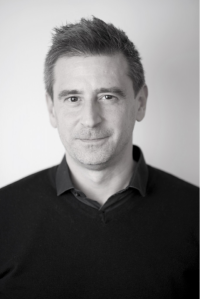
Lean Management is an approach that seeks to increase the degree of added value in a given activity. This is analyzed by all the company’s stakeholders, with regard to the expected level of performance they have set themselves. Let us take the example of a medical examination in a hospital setting: for the patient or the nursing staff, the main value is to obtain an answer to their health queries from the doctor. Achieving this objective is often preceded by several steps that can either generate value (e.g. medical imaging, physiological tests, electronic payment, etc.), or waste, (e.g. waiting time, excessive or duplicate administrative procedures, difficulty in finding one’s way around the hospital, etc.).
The purpose of Lean Management is therefore the overall efficiency of operations and the organization. It is obtained by maximizing the real added value of an activity by shortening the steps that are unavoidable, but without intrinsic value (in our example, the administrative steps) and by eliminating waste (waiting, errors or misinformed choices, unnecessary travel or transportation, excessive inventory, etc.)
There seems to be an abundance of support services in the Lean Management field; how can we go about making the right choice?
Lean Management relies on an unregulated certification system which is therefore specific to the organization that issues them, thus requiring particular attention to the choice of structure and methods of certification. The practical dimension of certification is essential. A minimum of operational experimentation is necessary to be able to mobilize the theoretical knowledge acquired and, above all, to integrate it into the specific reality of a company. This is particularly true for the sustainable implementation of solutions, and more specifically, for the human aspects. The acuteness and globality of such an approach can only be acquired through contact in the field: 80% of what I learned in theory, I relearned in the field! The value of the certification obtained therefore heavily depends on the educational content and teaching, as well as its relevance in a changing world (with regard to social challenges, digitalization, etc.). In my opinion, these are crucial elements to take into account when choosing a training program, because the real quality and actionable contribution of a certification (green belt or black belt) varies greatly from one organization to another.
Today, we speak more about Operational Excellence and Performance Approaches, as Lean Management has been hybridized with other methodologies, such as Six Sigma, Business Agility, and the Theory of Constraints. Behind the varying terminology, the fundamental principles are the same. Unfortunately, the goal is also to distance ourselves from the misuse of Lean Management for short term profit (for reducing costs and total payroll, for example). It is imperative to note that a Lean Management approach that does not thoroughly integrate the social or human factors can never lead to a solid collective ownership, nor, therefore, to sustainable results. Moreover, this choice invariably leads to financial miscalculations if we analyze the immediate and short-lived gains versus the costs incurred in the long run. The power of Lean Management lies first and foremost in a collective acceptance of what has value, and then in a consistent day-to-day practice that consolidates everyone’s trust in the fact that the efforts are in the common interest.
At a time when CSR obligations and issues are weighing more and more heavily on companies, how does Lean Management take these dimensions into account?
Lean Management is participatory by nature. The human element is at the center of the approach. Added value is a joint construction of all the actors who contribute to the development of a product or service; the customer, of course, with their satisfaction being the end goal, but also the managers, employees, suppliers, intermediaries, etc. A Lean Management approach capable of bringing added value that is exclusively focused on financial or economic aspects will not achieve global and long-lasting optimization objectives, nor will it lead to a mutually beneficial outcome. These benefits can only be achieved by incorporating the dimensions of sustainable and responsible development: namely social, economic, and environmental elements. There are still very few actors who incorporate all three of these dimensions into their certifications, despite it being a major societal issue. Today’s generations, who will be the policymakers and legislators of the future, have a clear awareness of the climate issues at stake, the depletion of resources, and even more so of the need to give meaning to their professional involvement.
Could you give us some concrete examples?
In a Lean Management approach, we use a tool to map the flows of a value chain, called VSM (Value Stream Mapping). The tool is not new, but what is new is incorporating elements of human-related/social and environmental waste. This makes it possible, for example, to identify inadequate material resources that contribute to increased CO2 emissions, to quantify the damage to society and to the company in financial terms, and to redirect its activity to new manufacturing procedures. This also allows us to evaluate human-related waste, and its cost to the company in terms of loss of motivation, absenteeism, and turnover. By integrating these values, and reasoning in terms of total cost, Lean Management continues to be a powerful lever for change, both for companies and for society as a whole.
To conclude, what are the conditions for a successful Lean Management approach?
A successful approach is one that truly synthesizes the expectations of customers and of all the company’s stakeholders, and that meets these expectations in an optimal way. A wide range of benefits can be expected, including an improvement in the company’s economic and financial performance, but also increased customer satisfaction and loyalty, stability and durability of the social model, and vitalization of the creativity of the company’s human resources.
Determination, exemplary management, and an ongoing joint construction approach are essential factors for success. Involvement and empowerment at all levels of the company encourage healthy questioning around areas for improvement and a proactiveness in problem solving. In short, Lean Management is a dynamic that consolidates the company’s strengths and synchronizes the satisfaction of people and of organizations.